How to Choose the Right Pad Printing Silicone Pad and Key Considerations
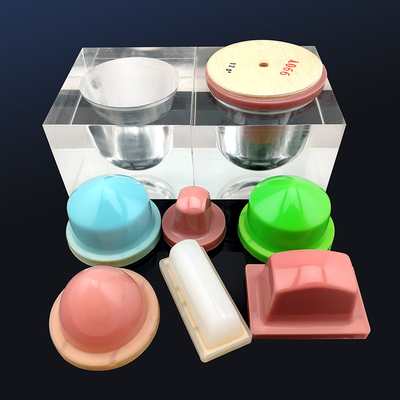
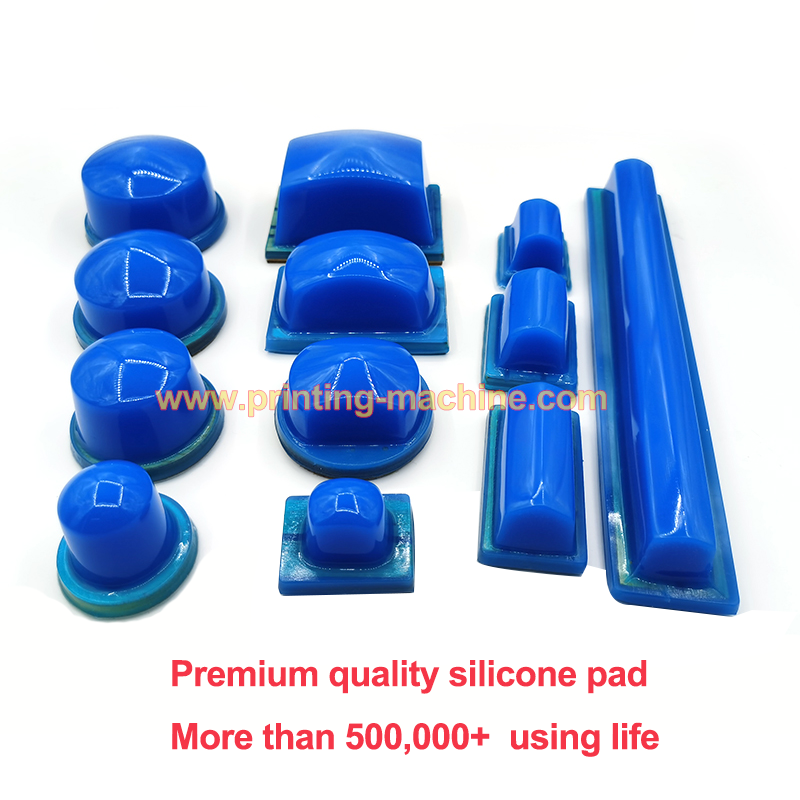
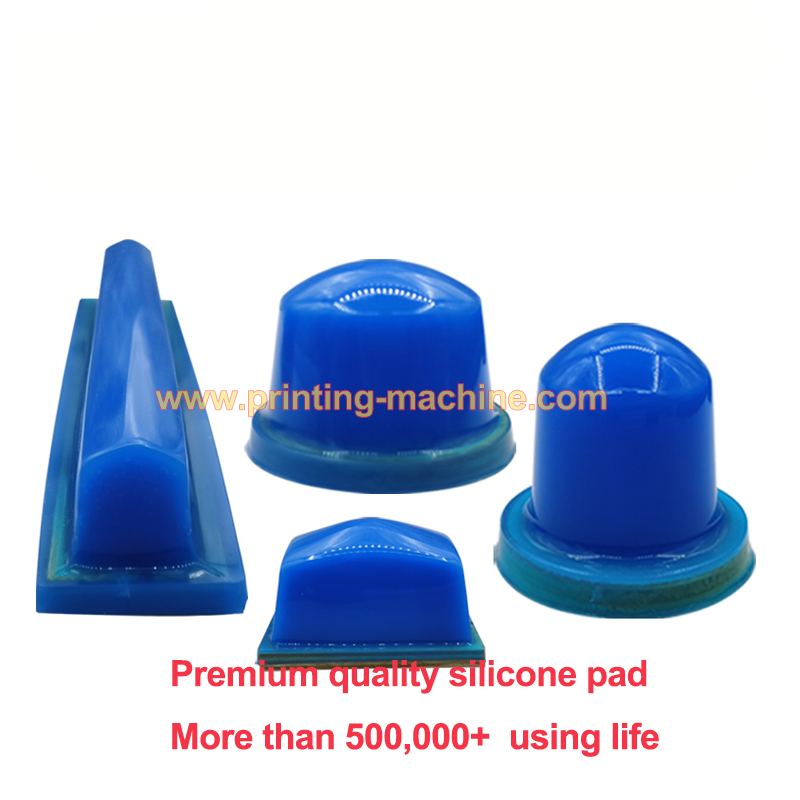
Key Factors for Choosing a Pad Printing Silicone Pad
Spherical Silicone Pad:
- Suitable for flat or slightly uneven surfaces.
- Advantage: Provides uniform contact area with minimal distortion of the design.
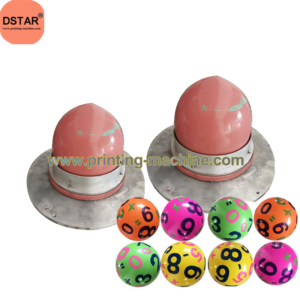
Conical Silicone Pad:
- Ideal for small patterns or curved surfaces, such as pen barrels or bottle caps.
- Advantage: Adapts well to curved surfaces and offers high printing precision.
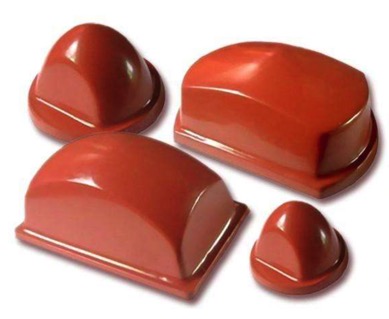
Elongated Silicone Pad for pad printing:
- Suitable for rectangular or strip-shaped patterns, such as nameplates or stripes.
- Advantage: Covers a larger area, ideal for large-format printing.
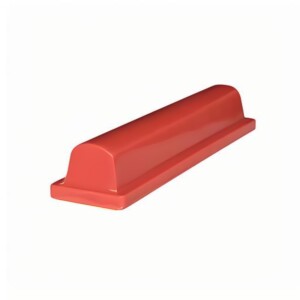
Custom-Shaped Silicone Pad:
- Designed for specific products, such as grooves, arcs, or irregularly shaped items.
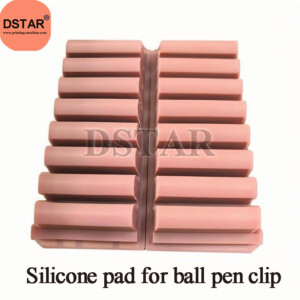
Soft Silicone Pad (Low Hardness, 20-40 Shore A):
- Suitable for irregular or complex surfaces, such as curved or textured surfaces.
- Advantage: High flexibility, better surface conformity.
Medium-Hard Silicone Pad (40-60 Shore A):
- Suitable for most standard printing scenarios, such as flat or slightly curved surfaces.
- Advantage: Balanced performance, widely applicable.
Hard Silicone Pad (60-80 Shore A):
- Suitable for fine patterns and high-resolution printing, such as small text or intricate lines.
- Advantage: Minimal distortion, ideal for high-precision printing.
The size of the silicone pad should be larger than the printed design but not excessively so:
- Too Small: Insufficient contact area, potentially leading to incomplete patterns.
- Too Large: Uneven pressure distribution may cause distortion or deformation.
Recommendation: The pad area should be 10%-20% larger than the design.
High-quality silicone pads should have the following characteristics:
- Good Elasticity: Quickly returns to its original shape after contact and release.
- Strong Solvent Resistance: Resists degradation from solvents used in the printing process.
- Anti-Static Properties: Reduces uneven ink adhesion on the pad.
The surface of the silicone pad should be smooth and free of bubbles to ensure clear pattern transfer.Surface texture can be adjusted based on requirements:
- Smooth Surface: Suitable for high-precision patterns.
- Matte Surface: Reduces glare and is suitable for large-area printing.
1. Match the Shape and Material of the Substrate
- Flat Products: Choose a smooth spherical or conical pad.
- Curved Products: Choose a soft or conical pad for better conformity.
- Textured or Uneven Surfaces: Use a soft silicone pad to ensure adequate contact.
2. Consider the Complexity of the Pattern
- For complex or detailed designs, select a harder silicone pad to minimize distortion.
- For simple, large-area designs, a softer pad may be more suitable for better coverage.
3. Consider the Type of Ink
- Some inks may be more aggressive and degrade silicone pads; choose pads with strong solvent resistance.
- For fast-drying inks, ensure the pad’s surface has good ink adhesion properties to achieve uniform transfer.
4. Consider Production Efficiency
- Select pads that are easy to clean and highly durable to reduce replacement frequency and improve production efficiency.
5. Test and Adjust
- Conduct multiple tests before production to ensure the compatibility of the silicone pad.
- Adjust the pad’s hardness, shape, or pressure based on the actual printing results.
Issue | Possible Cause | Solution |
Incomplete Patterns | Pad is too hard, insufficient contact area | Use a softer pad or adjust the pressure |
Distorted or Blurry Patterns | Pad is too soft, uneven ink transfer | Use a harder pad or adjust the shape |
Uneven Ink Transfer | Pad surface is uneven or has static | Replace with a smooth pad or use anti-static treatment |
Short Pad Lifespan | Aggressive solvents or improper cleaning | Use solvent-resistant pads and mild cleaners |
Choosing the right silicone pad for pad printing requires considering the shape of the product, the complexity of the design, ink characteristics, and production needs. Through proper testing and adjustments, you can find the most suitable pad to ensure high-quality printing results and production efficiency.Contact DSTAR Machine for professional pad printing proposal.
WeChat
Scan the QR Code with wechat