plastic bottle closure printing machine-Pad printing
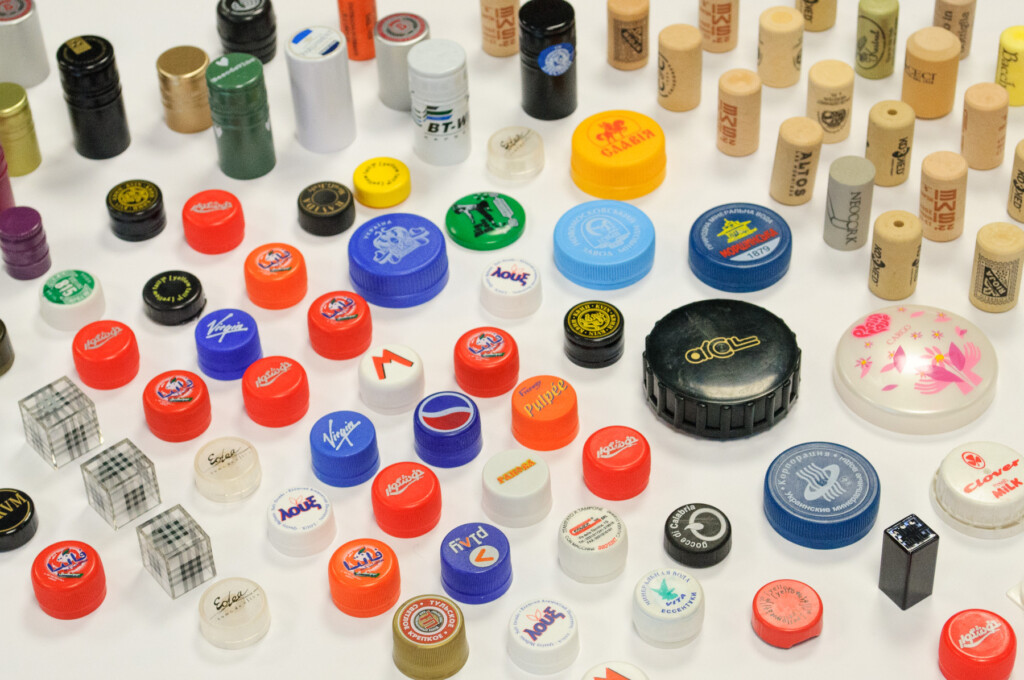
A plastic bottle closure printing machine is a specialized device used for printing designs, logos, or information onto the closures or caps of plastic bottles. These machines are designed to provide precise and consistent printing on cylindrical or curved surfaces. Here are some key features and considerations related to plastic bottle closure printing machines:
- Machine Type: There are different types of printing machines available for plastic bottle closures. The most common types include:
- Pad Printing Machines: Pad printing machines use a silicone pad to transfer ink from an etched plate onto the closures. They are versatile and suitable for small to medium-scale production.
- Screen Printing Machines: Screen printing machines use a mesh screen to transfer ink onto the closures. They are capable of high-speed printing and are suitable for larger production volumes.
- Digital Printing Machines: Digital printing machines utilize inkjet or UV-curable ink technology to directly print onto the closures. They offer fast printing speeds, high-resolution prints, and the ability to handle variable data.
- Printing Technology: Consider the printing technology used in the plastic bottle closure printing machine. Pad printing and screen printing machines are traditional methods, while digital printing machines are more advanced and offer additional benefits such as full-color printing and customization options.
- Closure Size and Compatibility: Determine the size range of closures that the machine can accommodate. Ensure that the machine is compatible with the specific closure dimensions, shapes, and materials (such as plastic, metal, or composite) that you intend to print on.
- Printing Features and Settings: Look for a machine that offers adjustable settings for ink density, printing speed, drying or curing time (for certain ink types), and registration accuracy. These features allow you to achieve precise and consistent prints on different closure designs.
- Automation and Control: Consider the level of automation and control offered by the machine. Some machines may have automatic feeding, positioning, and ejection systems to increase productivity. User-friendly control interfaces make it easier to set up and operate the machine.
- Ink Compatibility: Check the compatibility of the machine with different types of inks used for closure printing, such as solvent-based inks, UV-curable inks, or specialty inks. Ensure that the machine is designed to handle the specific ink type you plan to use.
- Maintenance and Support: Consider the maintenance requirements of the machine and the availability of technical support or spare parts. Regular maintenance and prompt support can ensure smooth operations and minimize downtime.
- Cost and Budget: Set a budget for your plastic bottle closure printing machine based on your business requirements and production volume. Compare prices, features, and capabilities from different manufacturers or suppliers to make an informed decision.
When considering a plastic bottle closure printing machine, it’s recommended to contact Shenzhen DSTAR Machine Co.,ltd get detailed information about the available options and find the best machine for your specific needs.
Here are some additional details about bottle closure pad printing machines:
Printing Process
Bottle closure pad printing machines utilize the pad printing process, which involves transferring ink from an etched plate onto the closures using a silicone pad. The pad collects ink from the etched plate and then transfers it onto the closure’s surface.
Machine Design
These machines are specifically designed to accommodate cylindrical or curved closure surfaces. They typically consist of a printing station, a rotating or indexing mechanism to move closures into position, an ink cup or ink tray for holding the ink, a doctor blade to remove excess ink from the plate, and a silicone pad for transferring ink.
Printing Station
The printing station is where the closure is positioned for printing. It may feature adjustable fixtures or clamps to hold the closure securely in place during the printing process.
Bottle closure pad printing machines often utilize a closed ink cup system. This system consists of a sealed ink cup that holds the ink and creates a controlled environment to prevent drying or evaporation. The ink cup features a ceramic ring or doctor blade that wipes excess ink off the etched plate before each printing cycle.
Plate Making
To print designs on bottle closures, you’ll need to create etched plates with the desired artwork or information. The plates are typically made from steel or photopolymer materials. The design on the plate determines the ink transfer onto the closures.
Ink Compatibility
Bottle closure pad printing machines are compatible with various types of pad printing inks. Common ink types include solvent-based inks, UV-curable inks, and specialty inks. The ink selection depends on factors such as the closure material, desired print quality, and curing requirements.
Registration and Setup
These machines offer registration systems to ensure precise alignment of the closure with the artwork on the plate. The registration system helps maintain consistent and accurate printing across multiple closures. The machine may feature adjustable settings for fine-tuning the printing parameters and achieving the desired print quality.
Production Speed and Capacity
Bottle closure pad printing machines come in different models with varying production speeds and capacity. The production rate depends on factors such as the machine’s design, setup time, closure size, and printing complexity. Some machines can handle high-volume production, while others are more suitable for small to medium runs.
Automation and Control
Depending on the model, some pad printing machines offer automation features such as automatic closure feeding, positioning, and ejection. User-friendly control interfaces allow operators to set up and control the printing process efficiently.
Maintenance and Support
Regular maintenance and cleaning are essential to keep the machine in optimal working condition. It’s important to follow the manufacturer’s guidelines for maintenance tasks and ink changes. Reliable technical support and availability of spare parts are also important considerations when choosing a machine.
When selecting a bottle closure pad printing machine, consider factors such as closure size compatibility, printing speed, registration accuracy, ink compatibility, and the machine’s overall durability and reliability. It’s recommended to consult with Shenzhen DSTAR Machine Co.,ltd to ensure you choose a machine that suits your specific requirements.
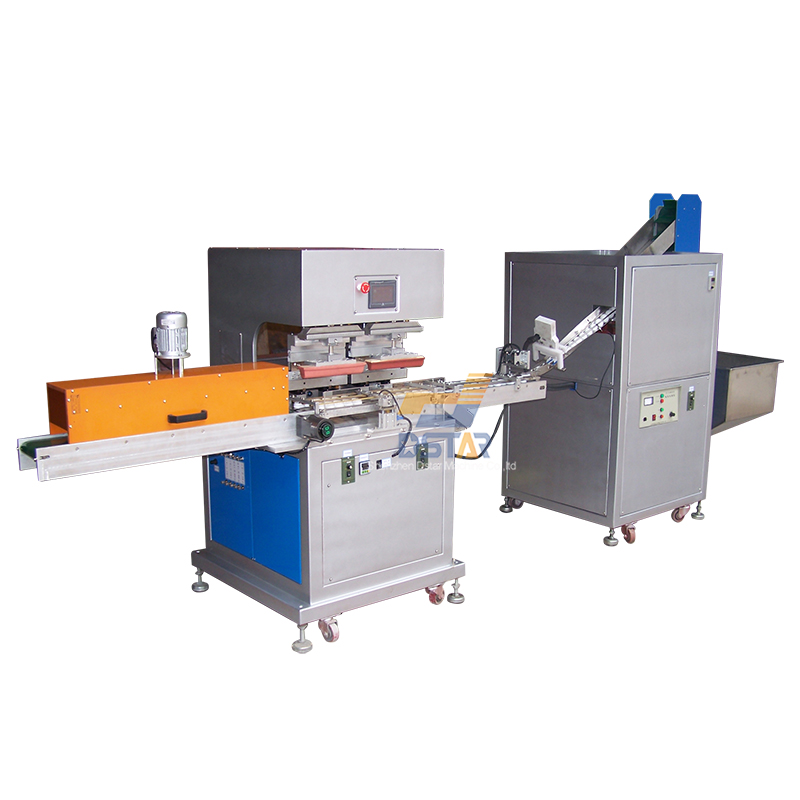
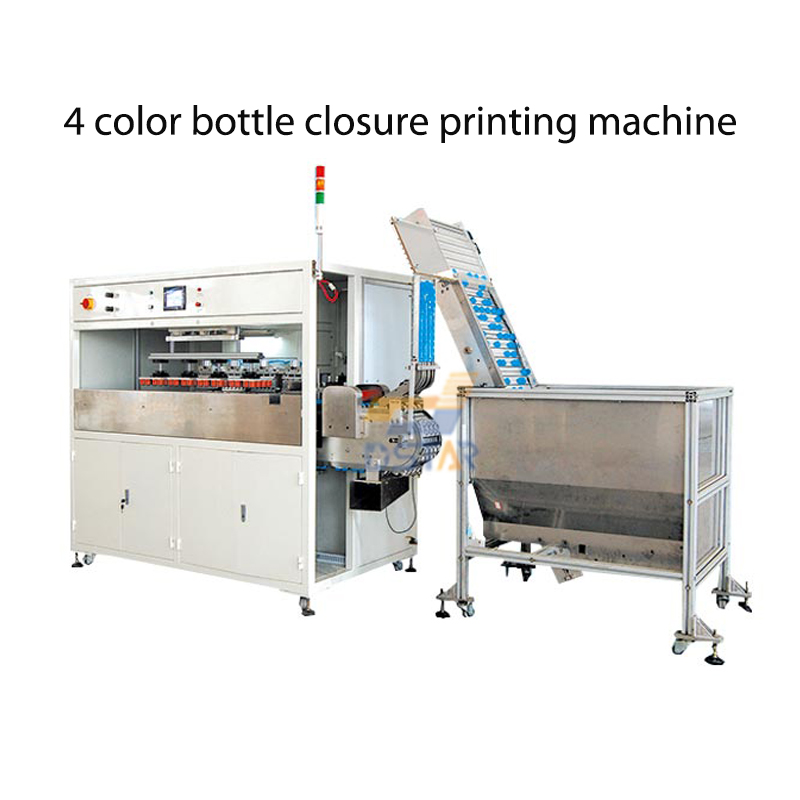
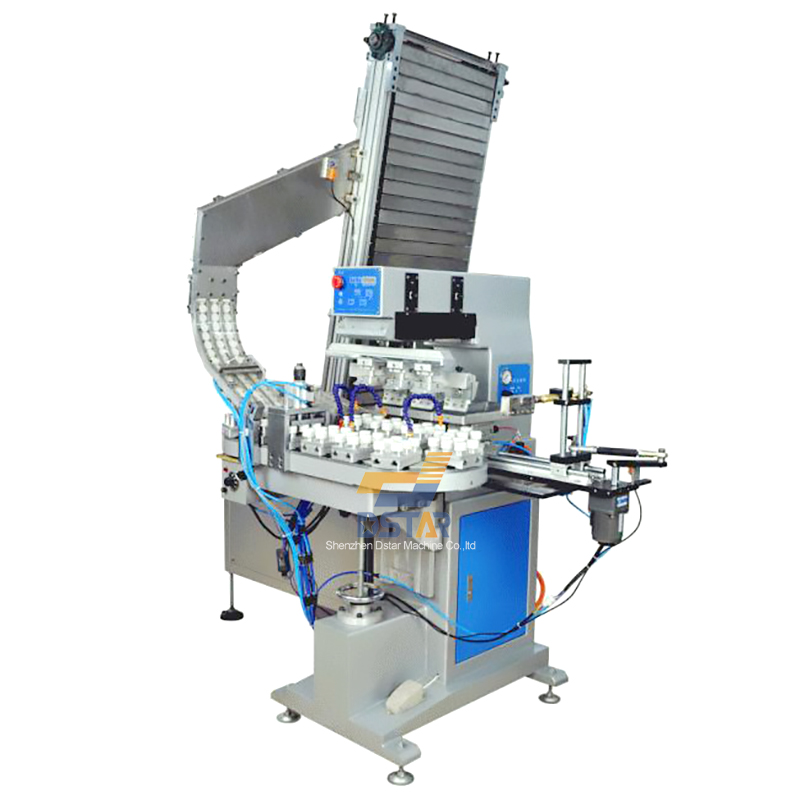
WeChat
Scan the QR Code with wechat